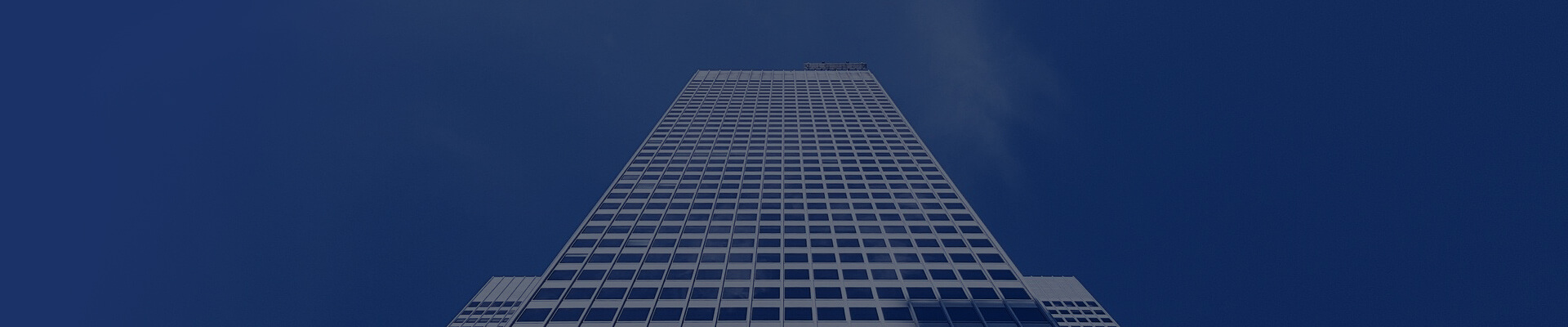
Newsroom
Building A Technical Platform—Raising Effectiveness of Automated Equipment Research
Release Time:2020-06-02
If there is a model in the initial stages of automated equipment development, it will be of great benefit to development of equipment design and model construction. If there is a verification platform before processing and production in the later stages of design, many unforeseen losses can be avoided. We have built two technical platforms for motion control and visual testing and produced more than 80 functional modules (covering technologies such as visual position grabbing, AOI detection, IoT communication, and robotic control) to meet the demands of our customers. Building a solution At present, the vast majority of platforms used by suppliers are essentially simple in nature and as a result cannot carry out complex and comprehensive experiments. They are also too small in size to verify our actual projects. In response to this, we decided to build a 2D and 3D comprehensive verification platform. The mechanical components of 2D comprehensive verification platform are built with a 4-axis high precision module (+/- 0.001), allowing all 2D and sectional 2.5D projects to be tested on this platform. The many different standard modules can be combined and replaced at will, and the platform can be used for pre-assessment or design demonstration of multiple projects such as assembly, polishing, moving, pasting, motion grabbing, positioning and assembly, image recognition, and image inspection. In visual aspect, it is composed of 600W-2000W area and line array cameras, a 4-path light source controller and various other light sources, such as strip light, coaxial light and surface light. It can be utilized in visual software development, feature extraction, barcode scanning, AOI test and other projects. Its control section is comprised of a PC + PCBA and a PLC + touch screen and can form a variety of control plans. The communication between the different control components can form a control circuit or a control circuit can be constructed separately. The 3D comprehensive verification platform's mechanical parts are built by 6-axis robots, and its vision capabilities are the same as the 2D platform except for added 3D camera. The 6-axis robot can move in any 3D space within the movable area. It has a high degree of integration and is very suited for use in building 3D platforms. The two platforms can use the same rack at the same time and can be docked together to create more complex experimental project. Platform application We have developed a proprietary software system with the 2D and 3D verification platforms. The system is developed on top of C# language WPT and consists of a system management module, vision module, core motion control layer, and user interface layer. These four parts complement each other to ensure that each module can be effectively utilized. The system management module has functions such as authority management, parameter setting, and the display of device operation information. The system obtains workpiece information with its specific algorithm, and then performs operations such as recognition, positioning, and detection to process the motion control parts. To date, we have developed multiple packaging modules based on robots and Table platforms for visual calibration, template matching, target tracking, etc., as well as visual engineering packaging modules such as barcode and 2D code reading, AOI detection, amongst various other modules. The core control motion layer is separated in to a control program and system function applications operating in a real-time environment. The control panel usually plays a key role in the overall platform software design and as a consequence its parts are usually packaged in DLL. The core motion control layer's functions include core data calculation and simultaneous data processing to ensure the use of multi-axis programs and to realize real-time system communication. The motion control layer implements the control functions of the robot and Table platform. Operation effect is usually determined by the user interface layer, user experience and user feedback are particularly important in this. This interface can realize the two-sided exchange of human-machine data to determine and display with its data and images whether the user has used the platform. Users can use the cameras to collect data, or change between automatic or manual modes with the interface to set movement speed and working mode. What’s more, the interface allows users to read device status information to analyze the current status and problems with the platform. Continuing to innovate We can use this platform to carry out multiple rounds of training for new staff. This means that new employees can learn about the basic operating functions and improve through practice. This has reduced the time needed for new employees to operate equipment skillfully from 6 to 3 months. In addition to this benefit, it has also shortened our equipment development cycle by 30% and reduced manpower by 50%. We will continue to expand 3D vision technology on surface screen detection and add additional modules in the future. This will help us give our customers the solutions that they need in the future.