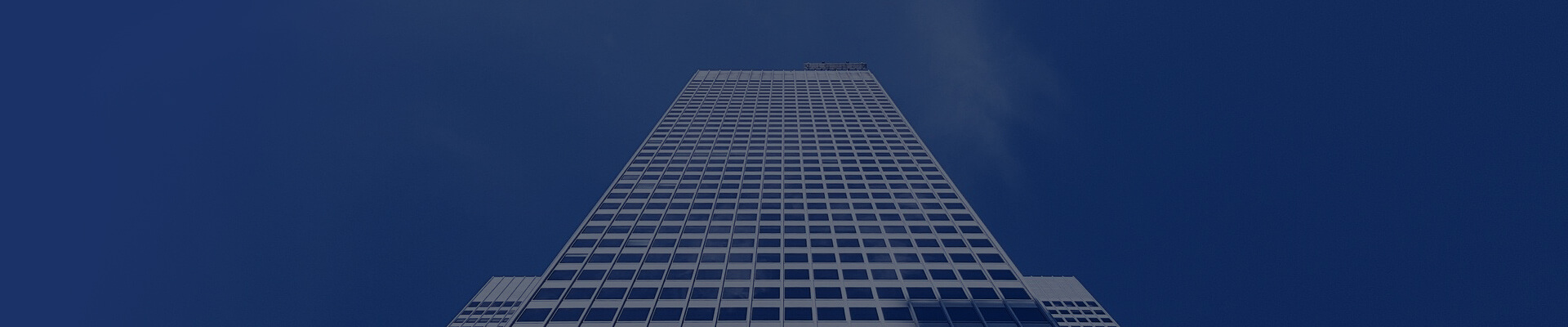
Newsroom
How Does The ESD Control Process System Protect Products?
Release Time:2020-04-30
ESD (Electrostatic Discharge) has been recognized as the number one cause of electronic product quality issues since the mid-1970s. As an enterprise leading the construction of electrostatic protection standards in the industry, how does our ESD process control system protect product quality? ESD Control Process is Crucial Statistics in recent years show that EOS (Electrical Over Stress) and ESD are the main causes of failure for IC-type device products, accounting for 58% of total failures. The global electronics industry loses over 10 billion US dollars every year due to ESD and EOS. As a result, the Chinese Yangtze River Delta region also suffers a billion yuan every year. In today’s age of the rapid development of automation and smart technology, it is necessary to sacrifice the static electricity tolerance (ESD Sensitivity, abbreviated as ESDS) of electronic devices to achieve high-speed, miniaturization and functional integration of electronic products. This implies that the ESD risk is critical to product quality. Providing Products with Full Protection As a leading global EMS company, Kaifa is fully aware of the importance of ESD control for quality. The ESD control system that we are currently using is built following the industry standards ANSI/ESD S20.20, which allows for comprehensive control of people, machines, materials, law, and environments. We also utilize smart systems and big data analysis to make up for any shortcomings of the traditional ESD control system and therefore offer better protection to product quality. Kaifa ESD Control System Module Basic R&D Module With 35 years of experience in electronic product ESD control, especially in magnetic head products that are highly sensitive to ESD, we have trained a high-quality team. This team is familiar with the ANSI/ESD S20.20 and IEC-61340 series standard and has participated in the formulation of national and industry ESD standards in the role of chief editor or editor-in-chief. This has given the team the ability to analyze ESD event mechanisms and protection principles deeply. They are responsible for the construction of the complete ESD control system, and are able to build an appropriate ESD control program according to the product’s ESD sensitivity level and process characteristics, as well as carry out the work for requirements definition, process & test method standardization, and scientific and practical protection methods and control methodology development as they continue to improve the system's level of completeness and effectiveness over time. Qualification Module With its advanced ESD testing equipment and professional team, our ESD laboratory has the ability to perform the plant infrastructure, materials, and equipment qualification following ANSI/ESD S20.20 requirements. For material qualification, we can perform the standard test under low humidity environment. We also develop a series of training material to ensure that all employees with different work position and rank have the right ESD knowledge and skill. On-site Control Module We customize different solutions to match the ESD sensitivity level of the products, process risks and customer needs. We also establish hierarchical control over the control standards, control items, and monitoring frequencies. We apply a self-developed iDAS (Intelligent Data Acquisition System) to sites that require the highest level of control. Meticulous ESD control is implemented with the collection of real-time ESD key control data, and the triggering of alarms in real-time reduces the latency of ESD risks. The use of on-site ESD key control data, personnel positioning, environmental status and plant production management system integration through data mining tools analyzes the relationship between ESD control and product quality. Audit Module We have designed a multi-dimensional audit mechanism to ensure the effectiveness of on-site execution. With visual inspection and simple dragging, employee self-inspection can find any non-compliance at station in a timely manner. Inspections made by line leaders and QA personnel can detect blind spots in employee self-inspection. Quarterly audits led by the ESD laboratory use the self-developed ESII (ESD System Integrated Indicator) to conduct company-wide system performance reviews. ESII evaluates the four aspects of on-site compliance, training, records and real-time monitoring system data performance. Based on the importance of each system module, level of risk, probability of problem occurrence, and coverage, weight distribution is implemented within the system to ensure the rationality of the system review. At the same time, we implant FMEA thinking into non-compliance risk assessment and use the three-dimensional methodology of severity, probability of occurrence and detectability to measure and ensure the fairness of the system. In terms of score statistics, and use conformity within the evaluation range to measure the implementation of the ESD system in each business part to guarantee the fairness of the evaluations. Failure Analysis Module Our highly skilled failure analysis team has over 20 years’ experiences in electronic product failure analysis. Through the use of advanced nondestructive CT and C-SAM flaw detection, EMMI leakage detection, liquid crystal hot spot detection, and other detection methods, they can carry out systematic EOS/ESD mechanism analysis for products and components, and locate and verify the root causes and risk points of EOS/ESD. The Future is Here Smart manufacturing is already racing towards us at breakneck speed, and enterprises must adapt to this trend if they want to develop. With this in mind, we are also speeding up the upgrade from reactive management to predictive management. There is still so much to be done; Deepening real-time monitoring, building a good data environment, connecting the currently isolated ESD system to other systems, using big data analysis to find hidden associations between ESD and quality and management, and integrating big data and production processes are what we should strive to achieve in the future.